The few raw materials which are placed in the export market take months rather than weeks to find their way to America. This has gone on to trigger steep price hikes, particularly for the raw materials utilized to make epoxies and resins. This is also the case for almost all sorts of coatings across the board including those in use in the automotive, aerospace, and even industrial sectors. The ultimate result of this unprecedented supply chain crunch is these high prices are being passed down to consumers. Since the latter part of 2020, epoxy prices in the United States have doubled and, 2 years on, show no signs of leveling off.
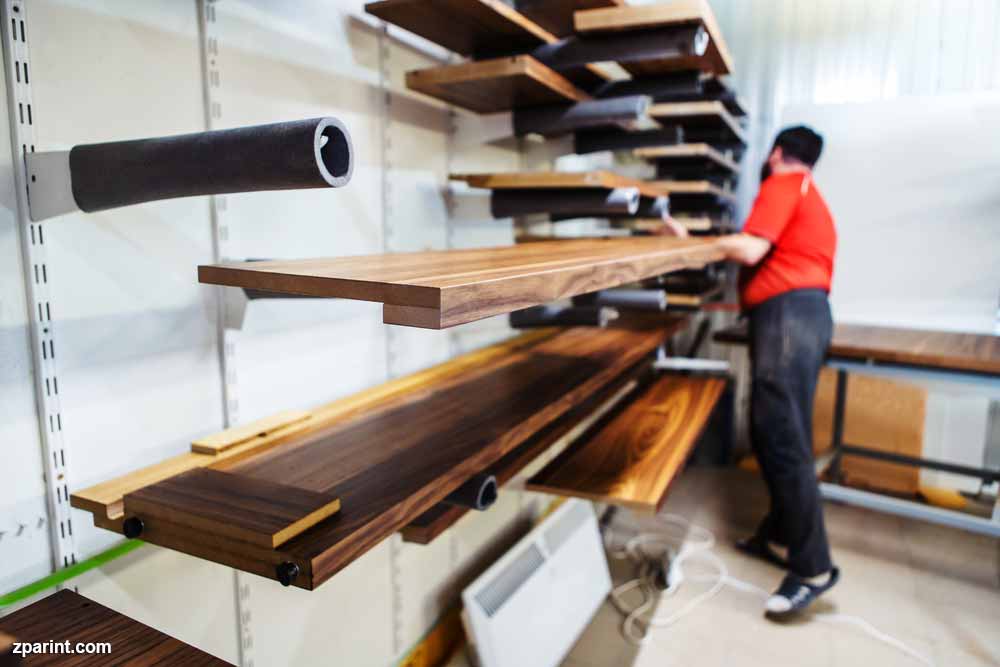
What are the factors that are complicating the American coatings supply chain issue?

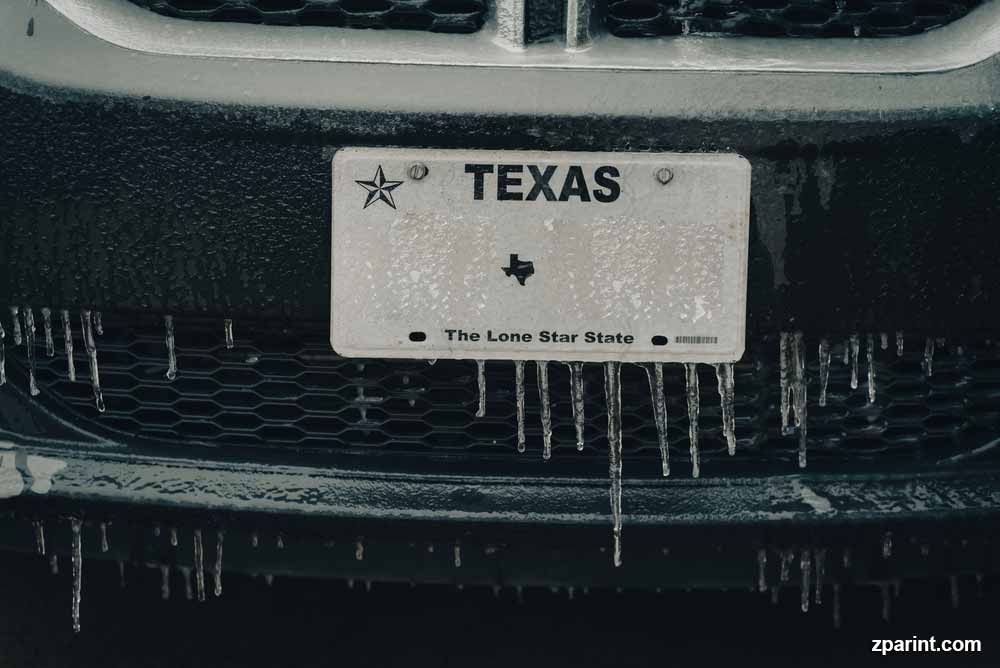
ZPar International is a leading US manufacturer of paint booth, spray booth and spray paint booth solutions that integrate cutting-edge coating technology and airflow patterns. We also offer a variety of quality powder coating solutions and paint booth accessories and equipment including abrasive blasting units.