Powder coating has become a popular choice for various industries due to its durability, versatility, and environmental benefits. However, achieving a high-quality, long-lasting finish relies heavily on one crucial factor: temperature control.
Throughout the entire powder coating process, from preheating to curing, maintaining precise temperatures is essential for optimal results. In this blog post, we’ll explore the critical role temperature plays in each stage and how you can optimize your paint booth for maximum efficiency.
Preheating: Setting the Stage for Success
The first step in powder coating is preheating the substrate. This vital step removes moisture and contaminants, ensuring a clean, dry surface for the powder to adhere to. The ideal preheating temperature depends on the material being coated but generally falls between 150°C and 200°C (302°F and 392°F).
Consequences of improper preheating:
- Moisture issues: Insufficient preheating can leave moisture trapped within the substrate, leading to blistering, peeling, and poor adhesion of the powder coating.
- Contamination: Incomplete preheating may not remove all contaminants, resulting in surface imperfections and a compromised finish.
Powder Spray Booth: Maintaining Optimal Conditions
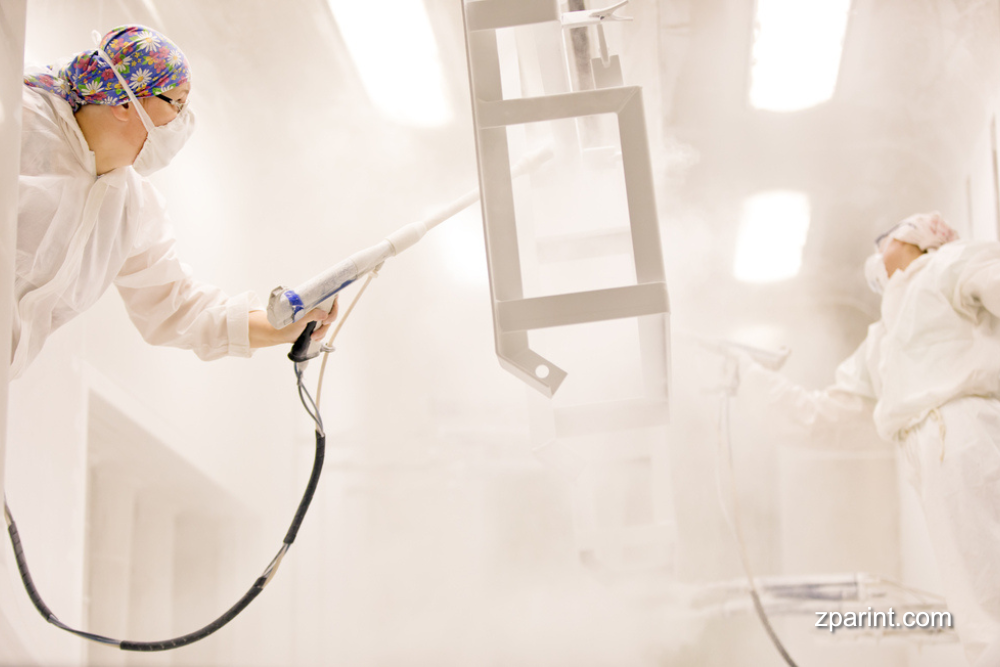
Ideal spray booth temperature:
- Room temperature: This is generally sufficient for most powder types, typically ranging between 18°C and 25°C (64°F and 77°F).
- Powder-specific requirements: Certain powders may require slightly higher or lower temperatures for optimal application. Always refer to the manufacturer’s recommendations.
Consequences of improper spray booth temperature:
- Powder clumping: Temperatures outside the optimal range can cause the powder to clump or become difficult to spray, leading to uneven coverage and wasted material.
- Reduced transfer efficiency: Incorrect temperatures can negatively impact the electrostatic charge of the powder, hindering its transfer to the substrate and increasing overspray.
Curing: The Final Touch
- Powder-specific requirements: Different powder types require different curing temperatures, ranging from 150°C to 200°C (302°F to 392°F). Consult the manufacturer’s instructions for specific recommendations.
- Curing time: The required curing time also varies depending on the powder and the thickness of the coating.
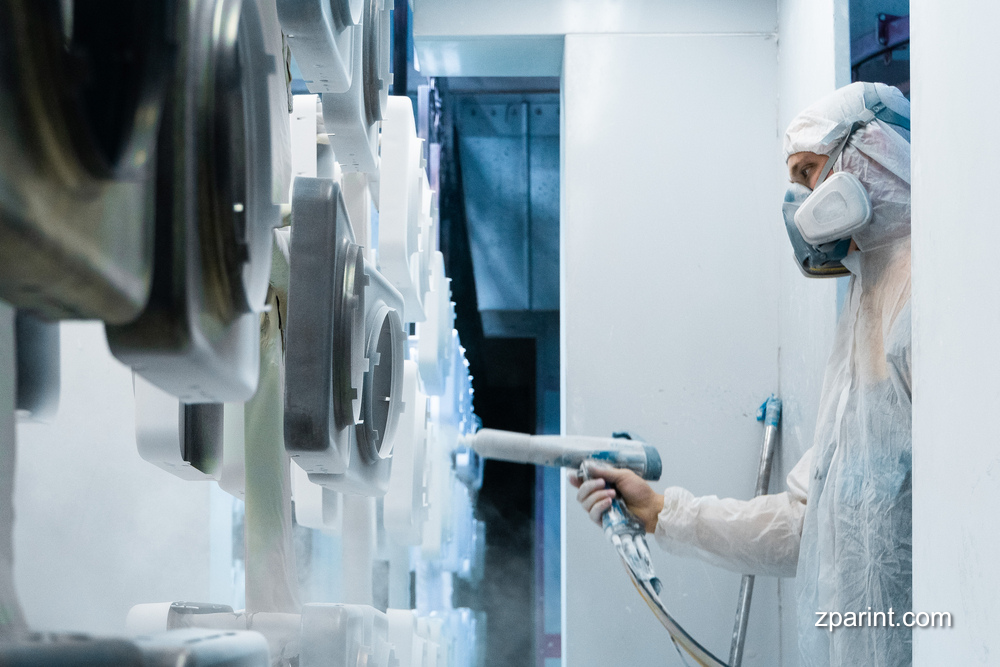
Consequences of improper curing:
- Incomplete curing: Insufficient temperature or inadequate curing time can result in a soft, uncured finish, compromising its durability and performance.
- Over-curing: Excessively high temperatures or prolonged curing times can lead to discoloration, brittleness, and reduced adhesion of the coating.
Optimizing Paint Booth Efficiency through Temperature Control
By understanding the importance of temperature control in each stage of the powder coating process, you can optimize your paint booth for maximum efficiency and achieve consistent, high-quality results. Here are some key considerations:
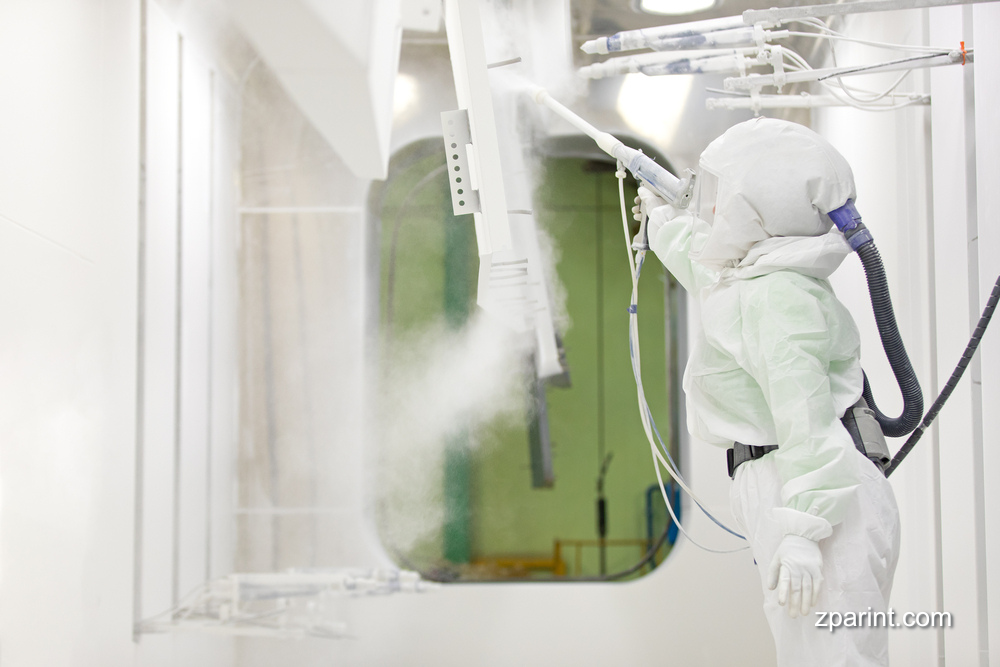
1. Invest in reliable heating and cooling systems: Ensure your paint booth is equipped with high-quality heating and cooling systems capable of maintaining precise temperatures throughout the entire process.
2. Implement paint booth thermal management systems: Consider incorporating advanced thermal management systems that monitor and regulate temperature automatically, ensuring optimal conditions for each stage of the powder coating process.
- Optimize paint booth airflow: Proper airflow is essential for maintaining consistent temperature distribution within the booth. Ensure your booth has adequate ventilation and air circulation to prevent hot and cold spots.
- Implement smart paint booth technology: Modern paint booths often incorporate intelligent control systems and sensors that monitor and adjust temperature automatically based on real-time conditions. These systems can significantly improve efficiency, reduce energy consumption, and ensure consistent, high-quality results.
- Train your staff: Educate your staff on the importance of temperature control in powder coating and provide them with the necessary knowledge and skills to operate the paint booth effectively.
By prioritizing temperature control throughout the powder coating process, you can achieve superior results, optimize efficiency, and minimize waste. Investing in reliable equipment, implementing effective thermal management strategies, and training your staff will ensure your paint booth operates at peak performance, delivering consistent, high-quality finishes for your customers.
Remember:
- Temperature control is crucial for successful powder coating.
- Each stage of the process requires specific temperature ranges.
- Implementing the right strategies can optimize efficiency and ensure high-quality results.
For expert guidance and solutions for your paint booth needs, partner with Zpar International. Our team of experienced professionals can help you achieve optimal temperature control and maximize the efficiency of your powder coating operation.
Contact Zpar International today to discuss your specific requirements and unlock the full potential of your powder coating process.