Powder coating has become a cornerstone of modern industrial finishing processes. This article will delve into what powder coating entails and why it has become integral in various industries.
Powder coating is a dry finishing process where finely ground particles of pigment and resin are sprayed onto a surface. The electrostatically charged particles adhere to the surface and are then cured under heat, forming a durable and attractive finish.
The evolution of powder coating techniques has played a crucial role in enhancing the durability, efficiency, and environmental sustainability of coatings. From its early methods to modern innovations, powder coating has undergone significant advancements.
Early Powder Coating Methods
In the early days of powder coating, flame spraying and fluidized bed coating were among the primary methods used.
Flame Spraying: Imagine trying to evenly paint a complex object with a blowtorch! Flame spraying involved heating the powder to its melting point and applying it to the surface using a flame gun. While effective, it often resulted in uneven coatings and material wastage.
Fluidized Bed Coating: Fluidized bed coating emerged as an alternative method, where substrates were preheated and then immersed in a bed of fluidized powder. The powder particles melted onto the surface, creating a uniform coating. Think of it like dipping a warm pretzel into a big tub of salt. However, controlling coating thickness proved challenging with this method.
Advancements in Powder Coating
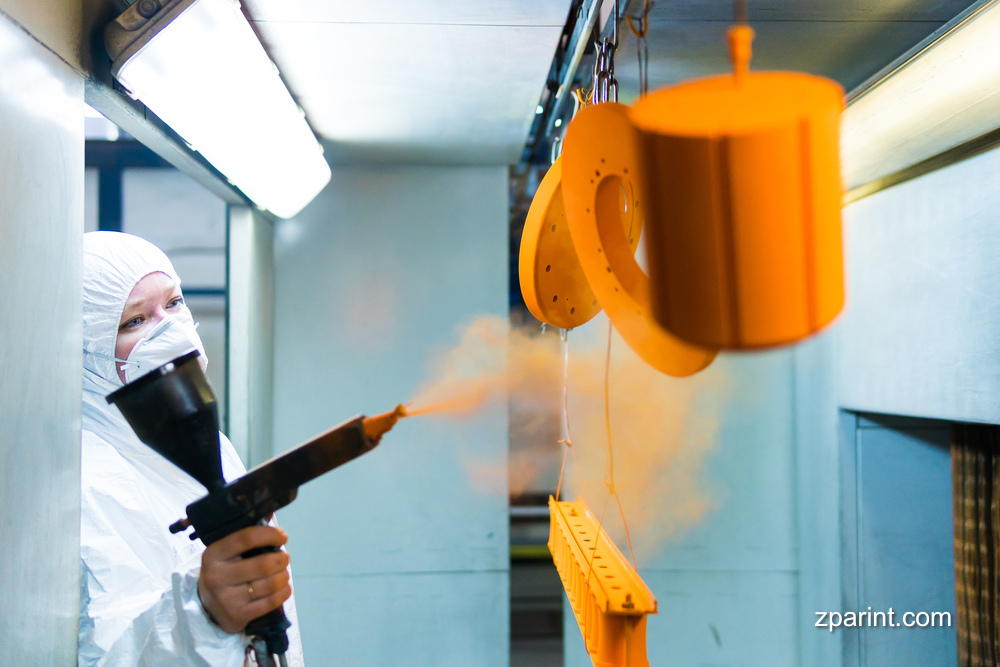
Technological advancements have revolutionized powder coating techniques, introducing specialized powders and application methods.
Thermoset Powders: These powders cross-link and solidify upon heating, providing exceptional durability and chemical resistance. Think of them like superglue for coatings – once they’re set, they’re incredibly tough! They are ideal for demanding applications such as automotive and aerospace components.
Thermoplastic Powders: Thermoplastic powders melt and fuse together upon heating, offering flexibility and impact resistance. Imagine a coating that can bend without breaking – perfect for things that get bumped around. They are suitable for applications requiring toughness and versatility.
Electrostatic Spray Applications: Electrostatic spray technology has significantly improved the efficiency and precision of powder coating. By charging powder particles as they are sprayed onto surfaces, electrostatic spray applications ensure better adhesion and coverage. It’s like those magnets that always stick together the right way – the powder clings exactly where you want it.
Environmental Considerations
Powder coating has become synonymous with sustainability in the coating industry.
Reduced VOC Emissions: Compared to traditional liquid paints, powder coatings contain minimal to no volatile organic compounds (VOCs). That means no more harsh chemical smells in the workplace and a healthier environment for everyone.
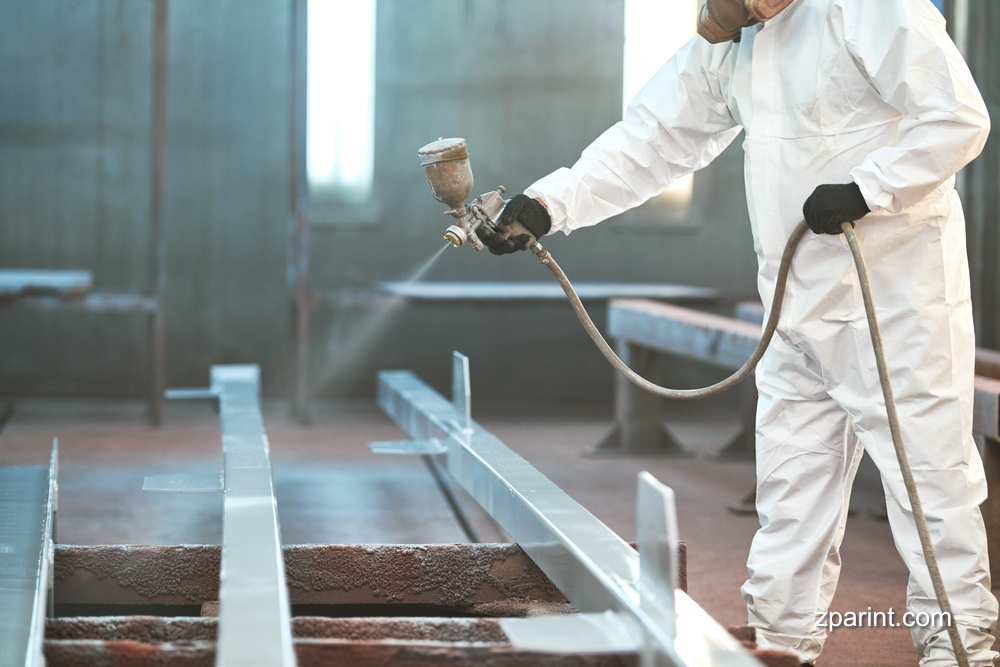
Minimal Waste Generation: Powder coating produces minimal waste, as overspray can be collected and reused. Imagine a project where almost all the material you use actually ends up on the product – that’s both efficient and good for the planet.
Energy Efficiency: Powder coating often requires lower curing temperatures than liquid paint, leading to energy savings and reduced greenhouse gas emissions. It’s a win-win: you save money on your energy bill and do your part to protect the environment.
The Shift to Sustainable Industrial Finishes
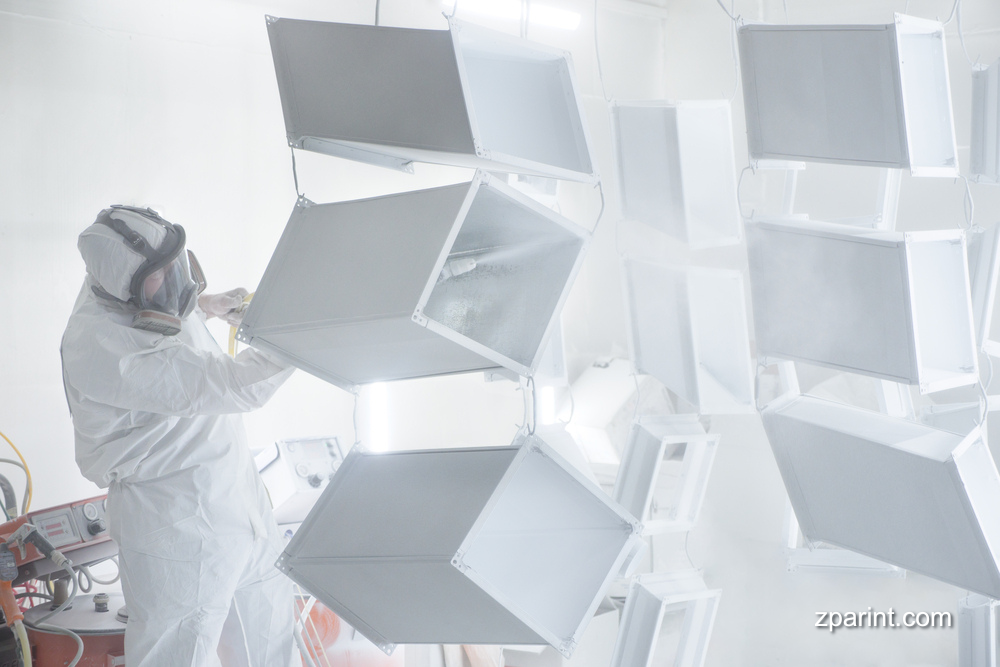
Powder coating has emerged as the leading choice for sustainable and efficient industrial finishes. Its durability, environmental friendliness, and aesthetic appeal make it the preferred option across various industries.
The evolution of powder coating techniques has transformed the industrial finishing landscape. At Zpar International, we’re dedicated to providing high-quality, sustainable coating solutions that meet the evolving needs of our clients.