In industrial manufacturing, the coating process is a crucial stage that can significantly impact the quality and durability of the final product. Whether you’re dealing with large machinery, automotive parts, or consumer electronics, choosing the right coating method can make all the difference in protecting your investment and ensuring customer satisfaction. We will help you navigate through the factors to consider when selecting the ideal coating technique for your specific industrial needs.
Understanding Your Options
Before diving into the details, it’s important to understand the various coating methods available. Common techniques include:
- Paint Booth: Utilized for liquid coatings, this method involves spraying paint onto the surface. It’s suitable for a wide variety of materials, including metals and plastics.
- Spray Booth: Often used for applying surface finishes, spray booths help contain the overspray and ensure even application. They’re particularly useful for automotive and aerospace industries.
- Powder Booth: Powder coating involves electrostatically applying a dry powder that is then cured under heat to form a hard finish. It’s renowned for its durability and environmental friendliness.
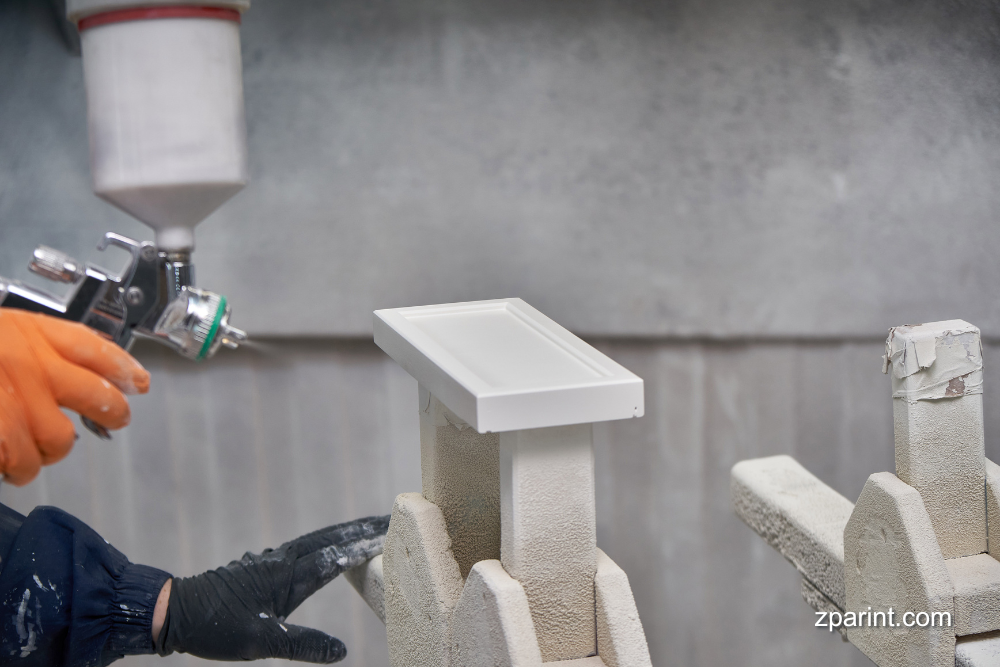
Key Factors in Selecting a Coating Method
- Material Type: The type of material you’re working with is a primary consideration. Metals, plastics, ceramics, and composites each interact differently with coatings. For instance, metals might require abrasive blasting before painting to improve adhesion, whereas plastics might need special primers.
- Environmental Conditions: Consider the operational environment of the coated product. Factors like temperature fluctuations, exposure to chemicals, UV radiation, and moisture can affect the longevity of the coating. Powder coatings are often preferred in harsh conditions due to their robust properties.
- Desired Finish Quality: The aesthetic and functional quality of the finish is crucial. Some applications might require a smooth, glossy finish, while others might need a matte or textured appearance. The choice between paint and powder coatings can influence the final look and feel.
Industrial Coating Processes and Equipment
- Paint Booth Efficiency: A high-efficiency paint booth can save time and resources by minimizing paint waste and reducing drying times. Look for booths with optimal airflow systems to maintain even pressure and remove overspray effectively.
- Industrial Coating Processes: Consider automated systems for high-volume production. Robotic arms in spray booths can ensure uniform application, reduce labor costs, and increase throughput.
- Optimal Equipment Settings: Configuring the correct settings for temperature, pressure, and spray patterns is essential for achieving the best results.
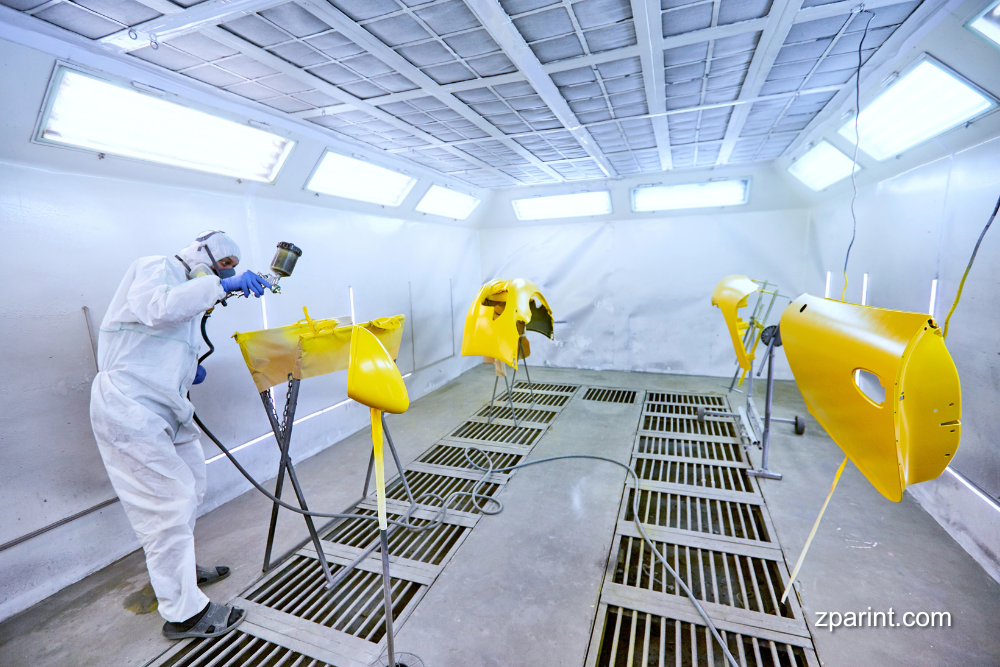
Application Method Selection
Selecting the right application method is not just about the coating itself but also about the equipment used. Factors like the size and shape of the components, production speed, and specific industry requirements should guide your decision.
For example, a batch oven might be the best choice for automotive parts that require precision and consistency, while an abrasive blast booth is ideal for preparing heavy industrial equipment for further coating.
Discover Excellence with Zpar
Selecting the ideal coating method for industrial applications is a multifaceted decision that impacts both the production process and the final product’s quality. By carefully considering the material type, environmental conditions, desired finish quality, and equipment efficiency, you can ensure optimal performance and durability in your coatings.
Ultimately, understanding and correctly implementing industrial coating processes can lead to enhanced product aesthetics, increased lifespan, and superior protection, benefiting your bottom line and customer satisfaction in the long term.
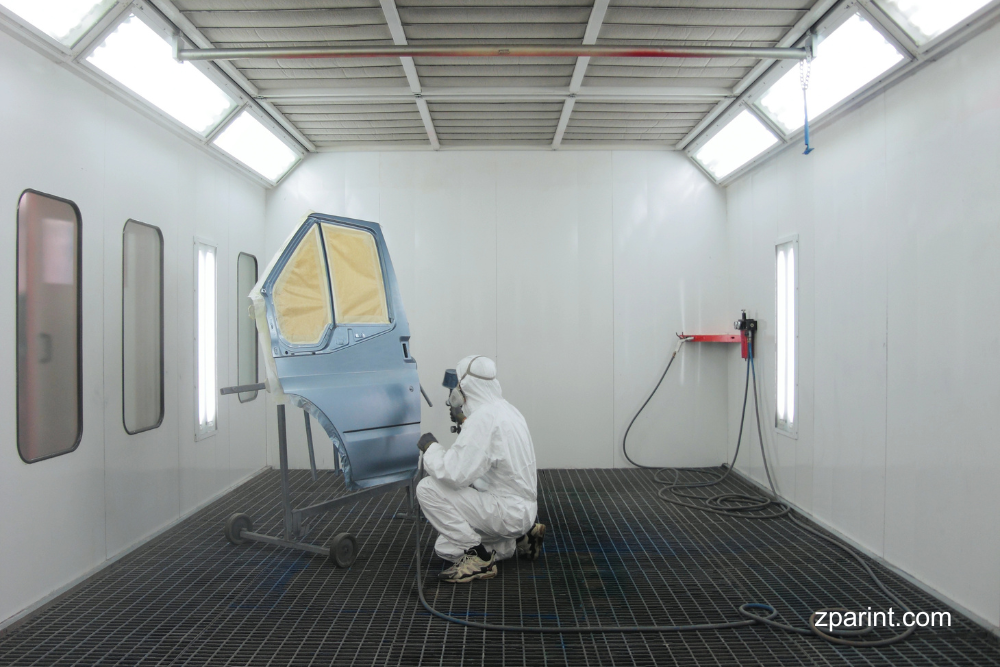
At Zpar, we take pride in providing exceptionally designed paint booths that cater to all your industrial coating needs. Our solutions are tailored to help you achieve top-quality results, ensuring your products stand the test of time. Contact us today to learn more about how we can support your coating applications with industry-leading equipment and expertise.