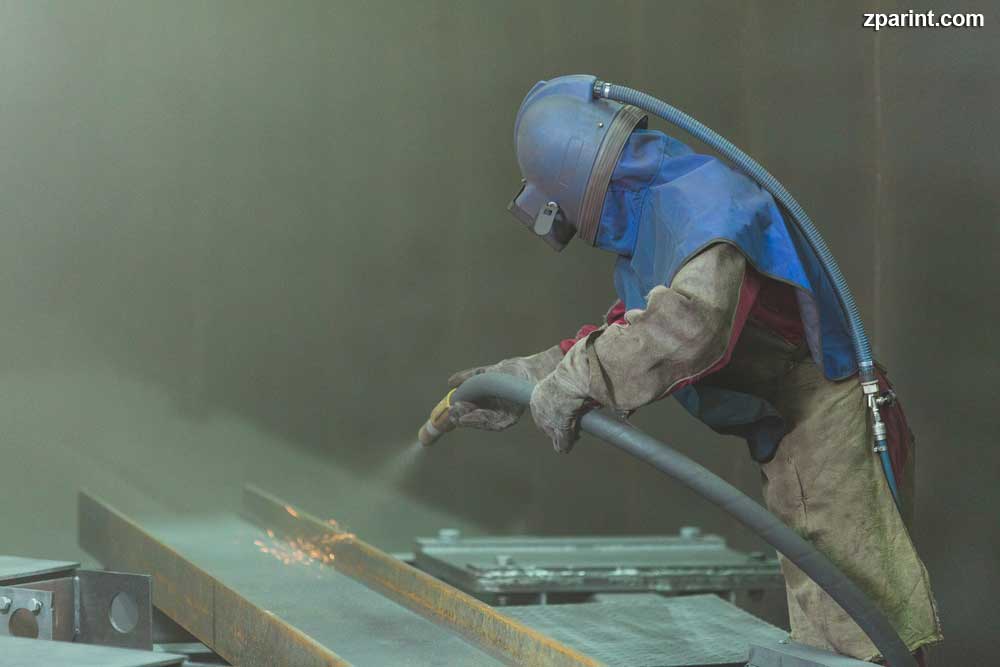
Abrasive blasting health risks
Abrasive blasting activities are known to create a lot of dust and even noise. At the same time, the abrasive material being utilized or the machinery being blasted can have toxic matter, that may include lead paint or even silica, both of which can pose serious health risks if inhaled by the workers. For example, silica sand might trigger breathing challenges, and in the extreme, lead to the development of serious diseases such as lung cancer. Coal slag and garnet sand have also been known to give rise to lung cancer.
On the flip side, copper slags, nickel slags, or even crushed glass can trigger serious lung damage. Alternatively, steel grit has the potential of triggering respiratory problems including lung damage. Additionally, some slags found within industrial machinery may carry trace amounts of toxic compounds including arsenic, cadmium, or even beryllium.
The high amounts of dust generated during abrasive blasting can, as well, be a serious cause of concern for employees. Dust buildup can impair the vision of workers and put them, along with others within their vicinity, at increased risk. Alternatively, abrasive blasting workers, or those in proximity to the area where it is performed, may ingest toxic substances if they aren’t wearing the right respiratory gear. For instance, trace levels of lead paint can remain in the air and cause lung challenges or even nervous systems problems. Additionally, as such health issues usually take long periods of time to develop, most workers never realize their health and wellbeing is at stake until it is sadly too late to act. On the other hand, depending on the materials being blasted, such clouds of dust might cause fire hazards if they contain flammable materials or the abrasive material being utilized is flammable. Lastly, abrasive blasting workers, and those within close distance to the area where it is executed, can sustain serious injuries since the blasting materials are expelled at very high velocities. Even when workers wear protective clothing or respiratory gear, they may still be at a heightened risk of sustaining serious skin and eye injuries.
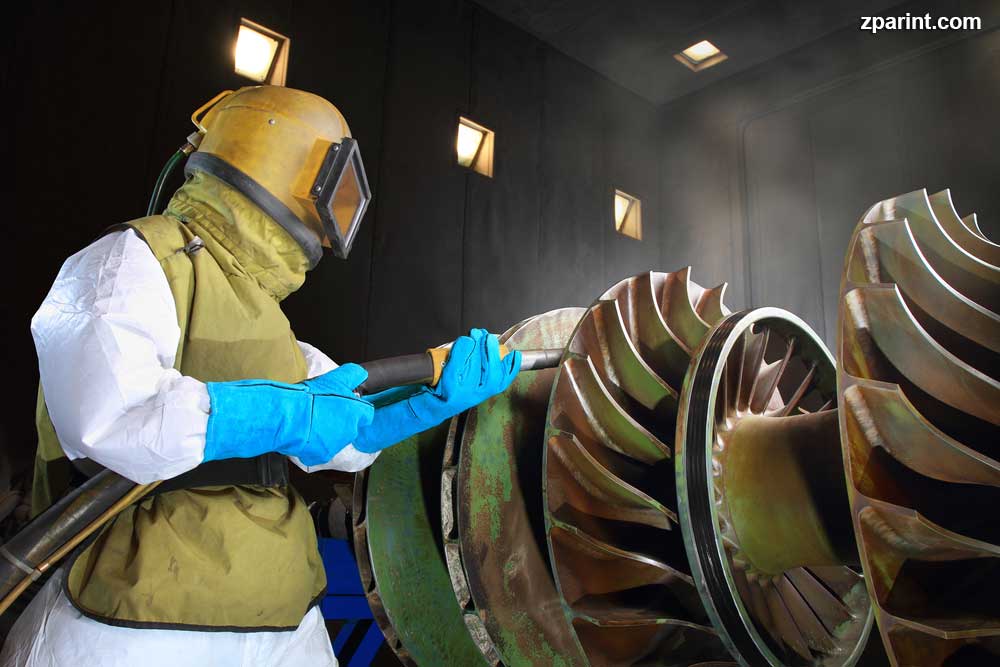
Protecting abrasive blasting workers against abrasive blasting materials
All abrasive blasting operations tend to be unique as they involve working on different surfaces, blasting materials and even the conditions in which they are performed. So, it is highly recommended prior to the job being done, you as an employer, should take the necessary time to determine all the risks involved. Also, you should appoint a knowledgeable worker trained to identify hazards and grant them the power to initiate immediate remedying actions to eliminate them if needed.
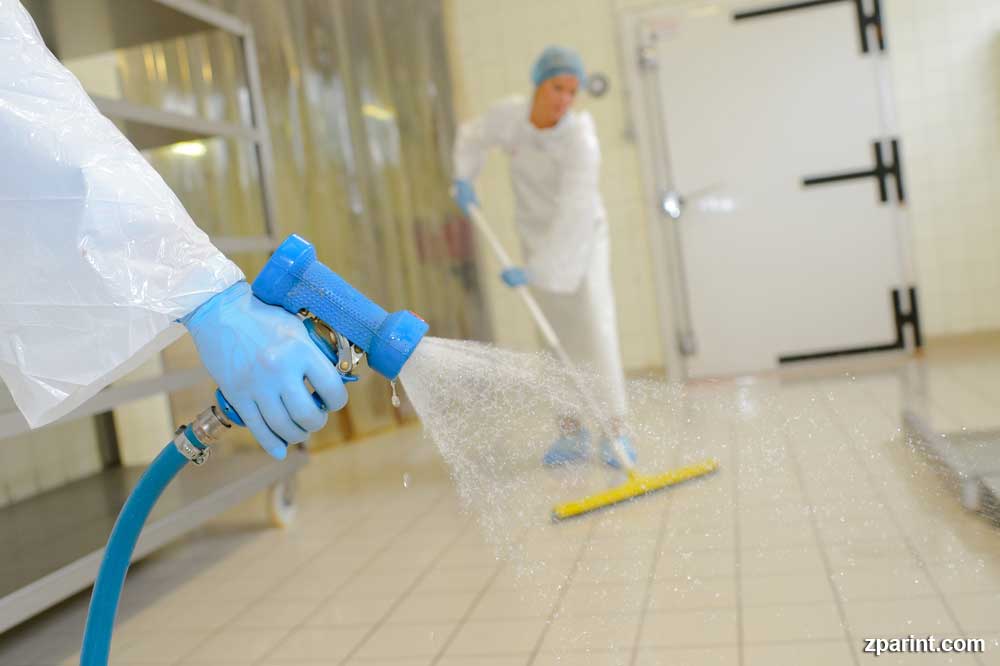
Administration controls
This set of abrasive blasting guidelines include enforcing good work and personal hygiene practices among your workers to significantly minimize their exposure to toxic matter. This includes carrying out regular wet cleanup methods or using HEPA filtered vacuuming to deter the buildup of toxic dust. Also, always ensure your workers never utilize compressed air for cleaning purposes since it creates dust buildup. On the other hand, ensure tarps together with other equipment are cleaned and decontaminated onsite.
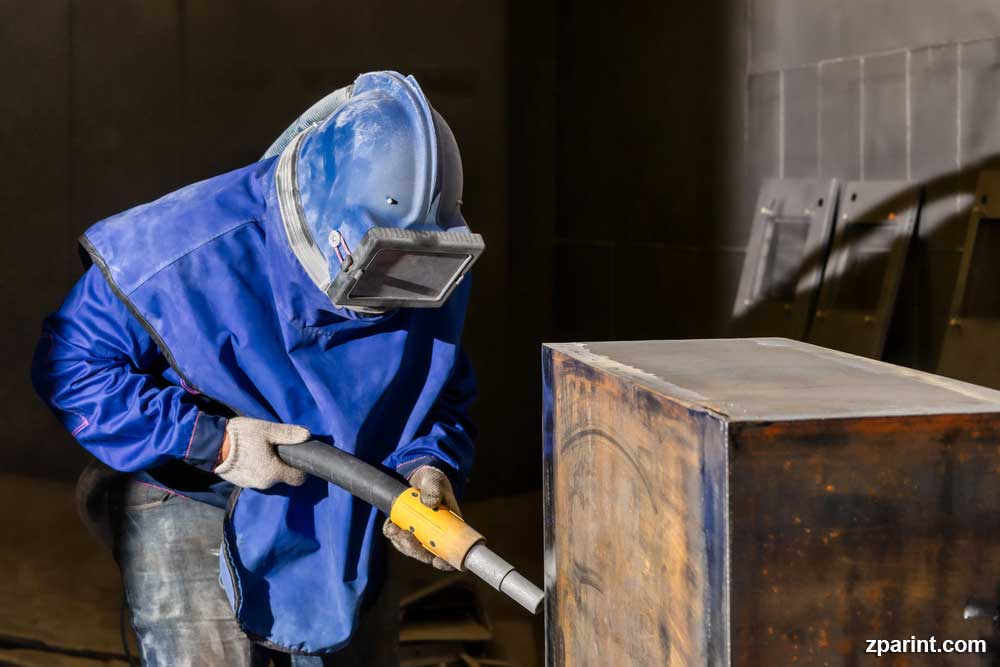
Abrasive blasting personal protective equipment (PPE)
Always make sure that your workers wear abrasive blasting respirators that can adequately cover their heads, necks and shoulders to effectively protect themselves against rebounding abrasives. Additionally, ensure you provide them with respirators that have been certified by NIOSH. Other PPE which should be utilized in abrasive blasting activities are hearing protection, eye and face protection, helmets, leather gloves and safety shoes or boots.
ZPar International is a foremost manufacturer of diverse abrasive blasting solutions that are widely acclaimed for their top-notch quality. We also offer paint booth, spray booth, and spray paint booth products. Give us a call today for a free consultation!