Abrasive blasting is an efficient and eco-friendly machinery and industrial equipment decontamination process. It sets to work by forcing a wide variety of abrasive materials under great pressure and velocities into the innards of diverse substrates. Apart from removing contaminants from the inner surfaces of industrial equipment, this process may also be utilized to create desired alterations to machinery surfaces. This can include smoothening rough surfaces or even roughening smooth surfaces. Abrasive blasting was patented in the late 19th century by Benjamin Chew. Since then, numerous techniques of this industrial process have emerged over time. With each delivering varying outcomes including the exact intensity of the desired results.
The abrasive materials used, otherwise known as blast media, tend to vary with each method. There are mild blast media such as walnut shells, crushed glass, corncobs, glass beads, coal slags, and garnets to name a few. On the other hand, there are yet gentler abrasive material solutions including soda, plastic beads, and even dry ice. Lastly, there are more aggressive blast media like aluminum oxide, steel grit, steel shots, and so on. When it comes to picking the best abrasive blasting solution for your unique needs and preferences, this will largely depend on the exact application and results you have in mind. Let us now take a closer look at some of the 5 most common abrasive blasting methods that are currently made available in the market.
1. Compressed air abrasive blasting
This is by far the most common variant of the abrasive blasting process. It goes to work by forcing compressed air and a wide range of blast media within the interior of machinery or industrial equipment. Once the chosen abrasive material is inside, it will then collide at great speeds with the surface, and in the long run, eliminate the contaminants present. Compressed air abrasive blasting has been comprehensively proven to be particularly effective in removing stubborn contaminants including corrosion along with weld splatter from the inner surfaces of diverse substrates. However, one of the biggest downsides of this form of industrial equipment cleaning method is it invariably creates a lot of dust buildup. This raises concerns over the safety and health of the operators or those in close proximity during the operation.
2. Wet abrasive blasting
As with compressed air blasting, wet abrasive blasting utilizes compressed air to propel the abrasive materials within the interior of machinery. What really distinguishes it from the former process is the use of water. The key advantage of wet blasting is its capability to greatly reduce the level of dust buildup. It is well noted for being able to soften the blast media used, which does away with the concern that its residues remain on the equipment’s inner surfaces.
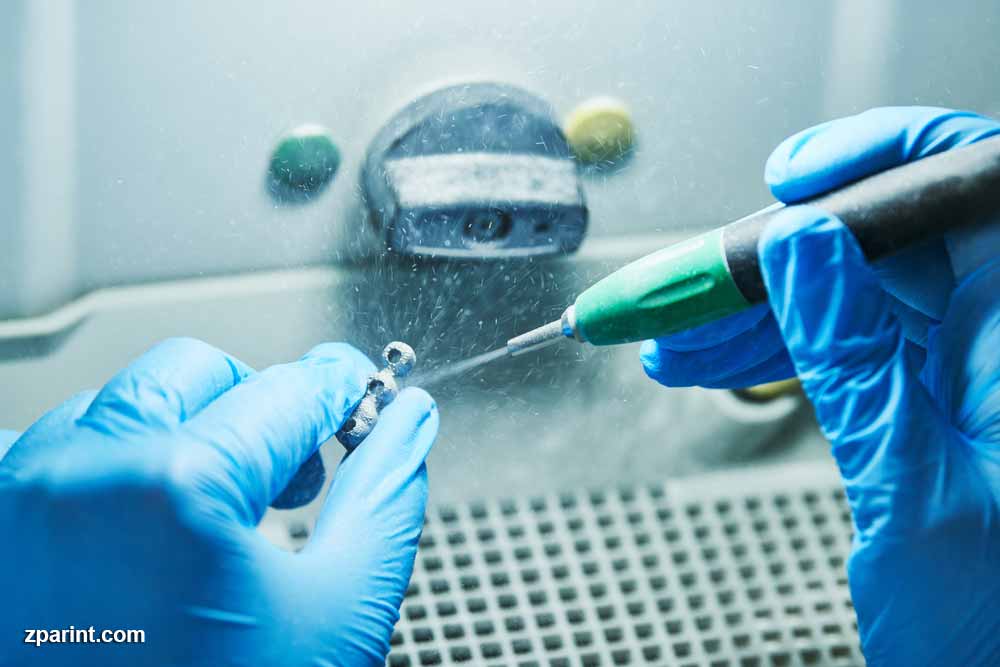
On the downside, wet abrasive blasting is known to corrode the surfaces being processed due to residual water. In such circumstances, you can include a corrosion-inhibiting agent in the water before performing the operation. Alternatively, you could line the surfaces with a corrosion-inhibiting solution as soon as the blasting is complete.
3. Dry ice abrasive blasting
Dry ice abrasive blasting makes use of dry ice pellets and compressed air to bring about the desired outcome. For those who might perhaps be in the dark, dry ice is the frozen form of the gas carbon dioxide. In this application, the dry ice pellets are forced into the innards of industrial equipment under great velocity and pressure. Once inside, these particles collide with the surface, trap, and eventually remove contaminants from the surfaces of the substrate.
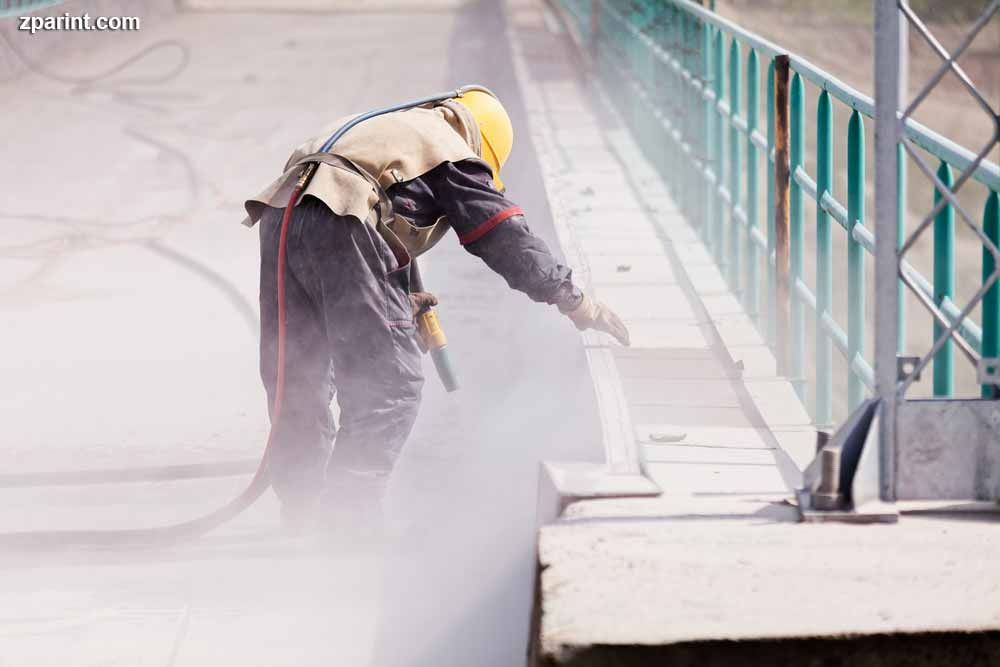
The key benefit of dry ice abrasive blasting is it leaves no residues of blast media after the operation. This is simply due to the fact that dry ice sublimates into gaseous form over time. In turn, this makes it especially suitable to safely decontaminate food-grade equipment and machinery. Also, it can ensure that the blasted surfaces undergo no damage, which is always a great concern with other alternative abrasive blasting methods.
4. Vacuum abrasive blasting
This abrasive blasting technique utilizes suction return systems to bring about the desired results. To this end, it can allow you to simultaneously blast contaminants from your machinery and safely collect the blast media you use too. Vacuum blasting is particularly suited for indoor blasting operations since it creates very minimal dust buildup.
5. Automated abrasive blasting
This type of abrasive blasting process may be used in diverse applications. This varies from automating a sandblasting cabinet to processing big industrial equipment via the utilization of robots. There are a number of factors you will need to consider before opting for automated blasting. This includes the uniformity of the inner surfaces of the substrates that need to be blasted, the exact number of them you wish to process at any given time, and the blast profile outcomes you desire.
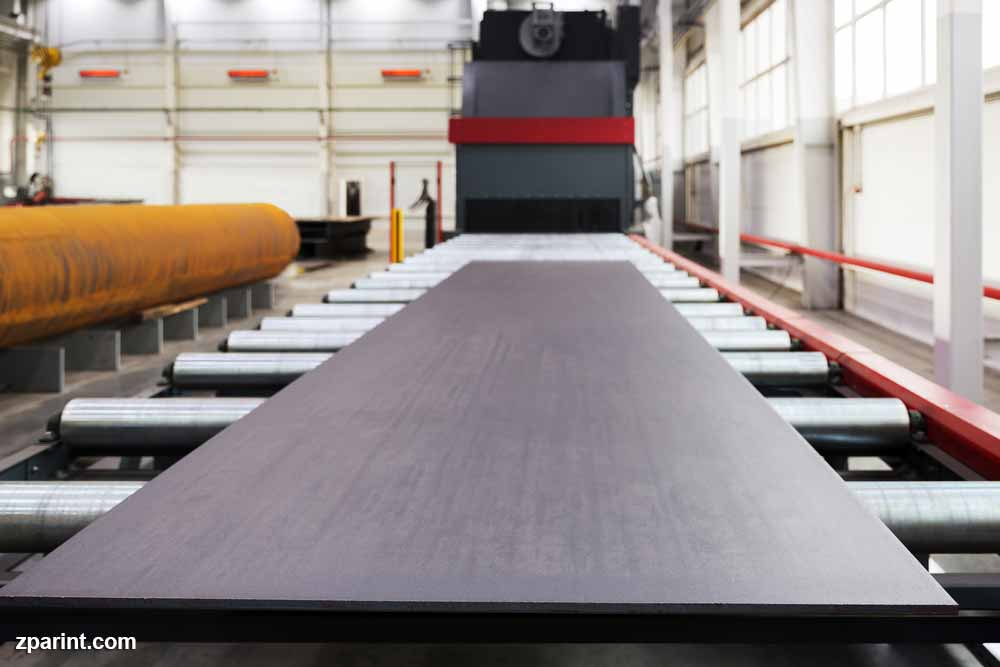
ZPar International is a leading manufacturer of abrasive blasting equipment including blast enclosures, dust collection systems, and more. We also specialize in manufacturing quality industrial finishing systems like paint booths, powder coating booths, and a variety of accessories. Give us a call today!