1. ignoring safety precautions
The use of power tools often comes with a number of safety concerns. So if you can’t observe all abrasive blasting safety measures, please stop. Nothing is worse than sustaining preventable injuries or grossly damaging your property or machinery. With abrasive blasting, there is always an inherent risk of bounce-back since it entails introducing blast media at high speeds and pressure. People in close proximity to the blast area are at risk of sustaining injuries if they haven’t donned on the right PPE.
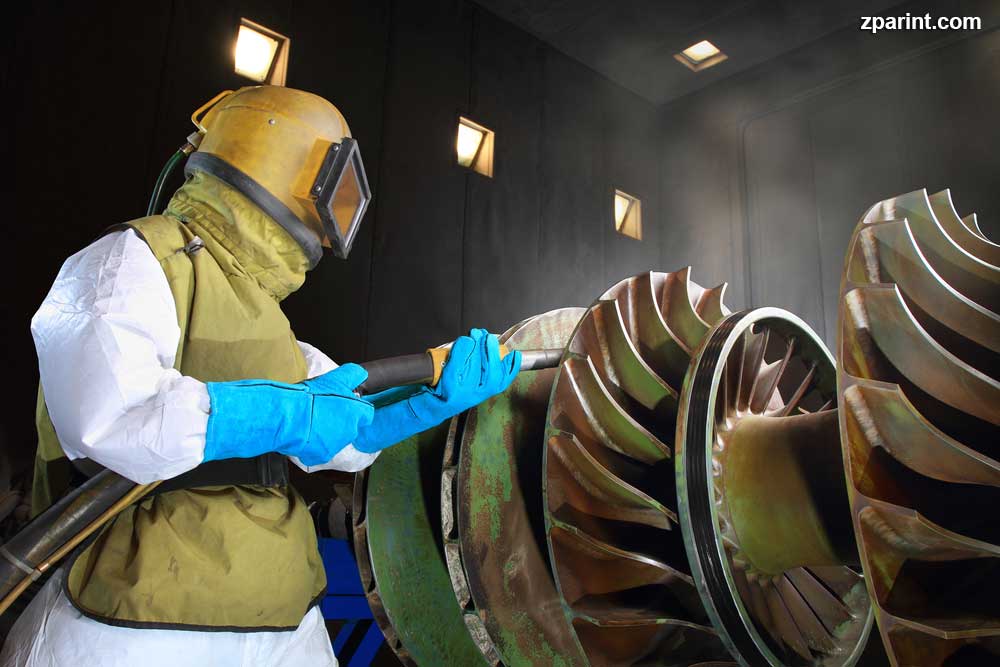
2. Making use of the wrong blast media
You will always be spoilt for choices when it comes to abrasive media you could use in your project. This includes glass beads, crushed glass, coal slags, walnut shells, steel grit, plastic beads, dry ice, bicarbonate of soda and more. However, it is important to note that different blast media are ideal for working on different surfaces and even different abrasive blasting projects. Should you have the misfortune to pick the wrong blast media, you could end up damaging your machinery or property.
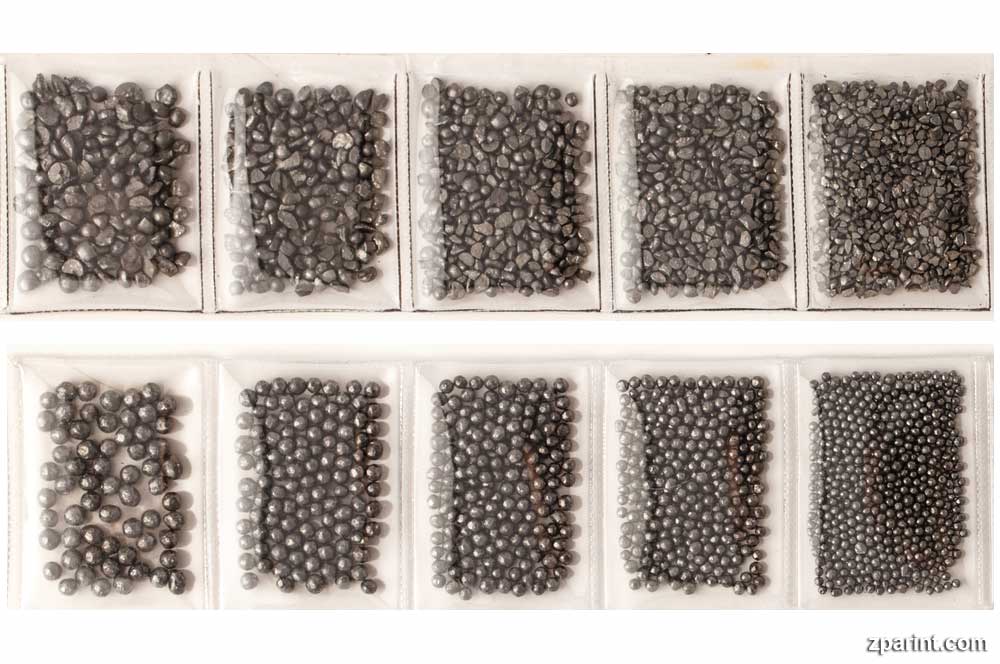
3. Failing to collect blast media after use
Ignoring to collect blast media after each abrasive blasting operation you undertake isn’t only impractical, but could be costly in the long term. This cleaning process should be always performed in a blast cabinet or if this isn’t possible, in a tarp enclosed area. This ensures you can easily collect the used blast media in a hassle-free manner. This way, you’ll have a convenient means of eliminating waste matter and capturing blast media for reuse.
4. Using the wrong sized blaster
Abrasive blasting units come complete with varying features and capabilities including power and size. The smaller and less powerful the blaster is, the more pocket-friendly it will be. Yet, the lower a blaster’s capacity is, the longer it will ultimately take to carry out an abrasive blasting project. Diminutive blasters need to be switched on and off repeatedly too. Should you be attempting a big cleaning project, a medium or industrial grade blaster will enable you to save time.
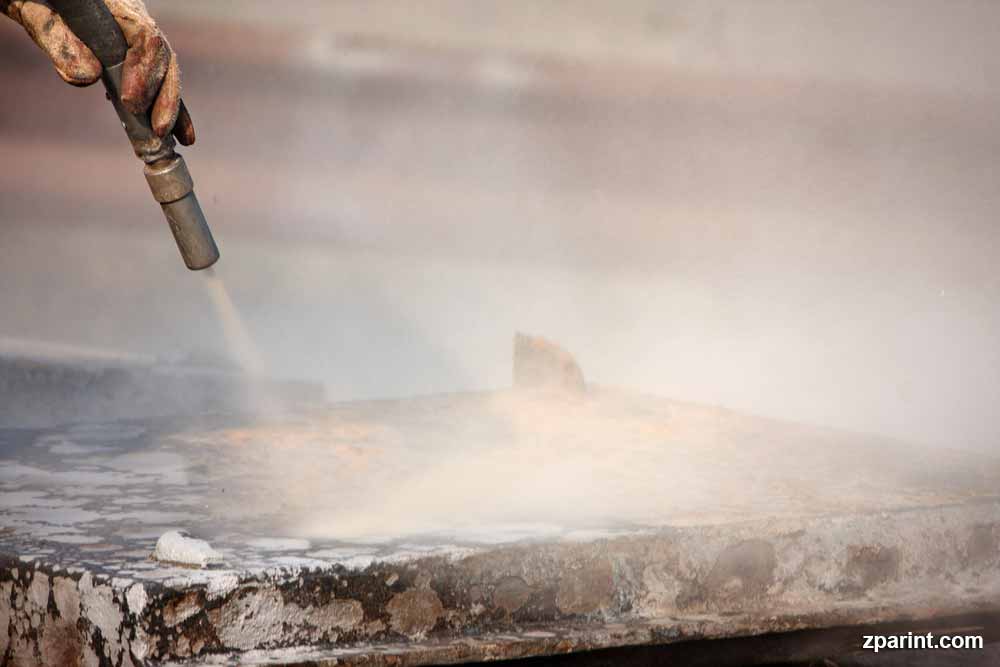
5. Failing to enlist the services of a professional when you feel you aren’t up to the challenge
It is always prudent to ask the help of a professional if the scope of your abrasive blasting project is too extensive or surpases your skills. This will go a long way in helping you avoid serious injuries or extensive damage to your property.
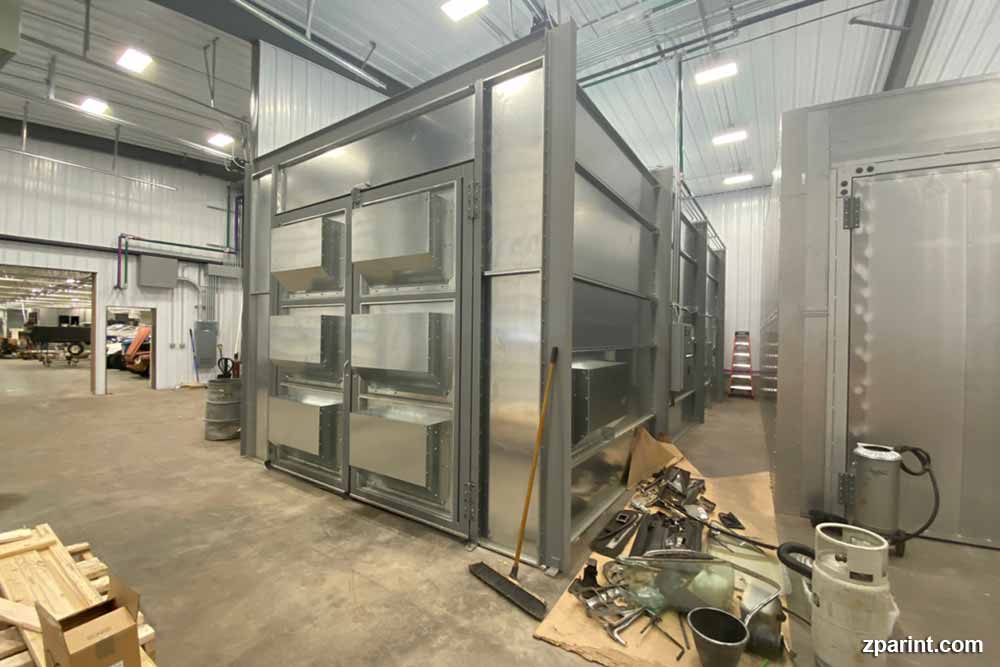
ZPar International is a foremost maker of top notch abrasive blasting units and equipment. We also offer paint booths and powder coating booths and other related accessories.